The number of waves or signals that occur in a fixed time interval specifies the frequency and it is measured in the units of Hertz (Hz). Based on the values of frequency, the frequency range is varied and it is determined. When the sound produced is at a higher level than the human hearing range, then it is said to be ultrasound, with a frequency spectrum of over 20KHz. The device that can generate or sense the ultrasound is called an ultrasonic transducer and ultrasonic sensor.
The various frequency ranges are Very Low Frequency- 3 to 30KHz (VLF), Low Frequency- 30KHz to 300KHz (LF), Medium Frequency- 300 to 3000KHz (MF), High Frequency- 3MHz to 30 MHz (HF), Very High Frequency- 30MHz to 300MHz (VHF), Ultra High Frequency- 300MHz to 3000MHz (UHF), Super High Frequency- 3GHz to 30GHz (SHF) and Highly High-Frequency Range (EHF) – 30GHz to 300GHz. This article gives a brief description of the working principle and circuit of an ultrasonic transducer.
What is an Ultrasonic Transducer?
Definition: An Ultrasonic Transducer refers to Capacitive Transducer or Piezoelectric Transducer that can convert electrical energy into ultrasound energy and vice versa. It is one of the types of sound-related transducers. The frequency spectrum range of this ultrasound or ultrasonic wave is over 20KHz and this is used at 200KHz based on the application.
These are used in non-destructive testing, measuring materials, and identifying small faults because of the lower wavelength of the ultrasound. These are important in sensors for level and flow measure, distance calculation, and also in biomedical, power, and other ultrasound applications. It has a wide range of applications in various fields.
Ultrasonic Transducer Working
When this transducer transmits the electrical signals onto the target, then the signal hits the object and returns to the transducer. Here distance of the object is calculated rather than the amplitude of the signal and sound quality. These transducers utilize ultrasonic waves to calculate a few parameters but are typically used in distance measurement.
This transducer depends on the sensitivity or resolution. The ability of the transducer to disconnect signals formed by the two close reflectors is called resolution. The ability of the transducer to detect the fault in the substances is known as sensitivity. An extremely damped transducer helps to lower the reflected signal and permits the transducer to study the closely spaced faults. To transducer should have higher resolution and sensitivity with large polarized ceramic materials and crystals to change its process.
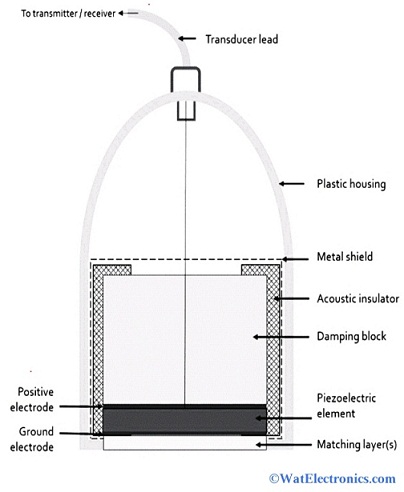
Ultrasonic Transducer Working
This system can receive and generate ultrasonic vibrations. It consists of a wear plate, backing, and an active element. A piezoelectric or the single crystal is an active element in the transducer that can convert or transforms the electrical signal energy into ultrasonic energy and also it can retrieve back the ultrasonic energy and converts it into electrical energy. A device called a fault detector generates the electrical pulse.
In non-destructive testing (NDT), this transducer transforms the electrical energy pulse generated from the test device into mechanical energy in the sound waves that move within the test device. The sound waves can be transmitted back from the test device to transform into an electrical energy pulse by the transducer that can be executed and demonstrated by the test system.
To produce and recover the sound waves at a higher frequency range and more than the human hearing level, the transducers act as ultrasonic speakers and microphones. This transducer is composed of a transmitter, receiver, control part, and power supply. The transmitter of this contains a transmitter and ceramic vibrator of about 15mm in diameter.
The function of the transmitter transducer is to transform the electrical energy of the ceramic vibrator into ultrasonic energy and radiates into the air. While the receiver transducer contains an amplifier circuit and an amplifier. It receives the sound wave/ultrasonic wave to generate mechanical vibration and transforms it into electrical energy.
This converted electrical energy is the output of this transducer receiver and it is used to detect the transmitted ultrasonic energy. The control section of this transducer controls the chain frequency of energy pulses, duty cycle, counting, distance detection by the transmitter, and sparse modulation. The power supply required can be DC 24V+-10% or DC 12V +-10%
This transducer uses the acoustic medium to detect non-contact and wear-free objects. They can identify any type of materials and substances like transparent objects, colored objects, metal and non-metal objects, solids, liquids, and also powdered substances. Its performance of detection is affected by environmental conditions like dust, smoke, water, etc.
The performance of this transducer depends on the manufacturing of the wafer and should have a large electromechanical coupling coefficient with high sensitivity. The operational frequency of this transducer is the piezoelectric material’s resonance frequency. The frequency of the applied AC voltage is equal to the resonance frequency of the chip, which has the highest output energy and the highest sensitivity.
Due to the high Curie point of the piezoelectric materials, the transducer uses low power and low operating temperature for diagnosis and works longer periods without any circuit damage. The medical ultrasonic transducer probes have high temperatures and require separate cooling equipment to prevent the breakdown.
Ultrasonic Transducer Working Principle
The sound wave is produced when an electrical signal is applied to an ultrasonic transducer and it vibrates throughout the specified range of frequency. These sound waves travel and will send back the data of the transducer (or reflection of the transducer’s echo) whenever any hurdle/interference appears. Hence the data is transformed into electrical signals.
The transducer determines the time interval between the transmitted sound wave and the received echo signal. The ultrasonic transducer working principle is based on the transformation of one form of energy to another form. The basic diagram of the ultrasonic transducer describing its working principle and the components is shown below.
At 40KHz, the ultrasonic pulse is transmitted by the ultrasonic transducer that travels through the air. This type of transducer is more preferred than any other infrared sensor because they are not influenced by dust, smote, black materials, etc. The ultrasonic transducers work efficiently in the suppression of noise distortion.
To evaluate the distance, the ultrasonic transducers utilize ultrasonic waves. The formula to calculate the distance is given as,
D = ½ * T * C
Where ‘D’ is the distance.
‘T’ gives the time gap between the transmitting and receiving of ultrasonic waves by the transducer
‘C’ is the sonic velocity
Ultrasonic Transducer Circuit
There are two main ultrasonic transducer circuits – one for the transmitter and the other for the receiver. They are designed with CMOS technology or a 555 timer. The ultrasonic transducer transmitter and receiver operate at the same frequency.
When the ultrasonic transmitter sends the ultrasonic waves towards the particular target and sound waves hit the object, then the sound signals are converted into electrical and ultrasonic signals. The ultrasonic transducer circuit for the transmitter is shown below.
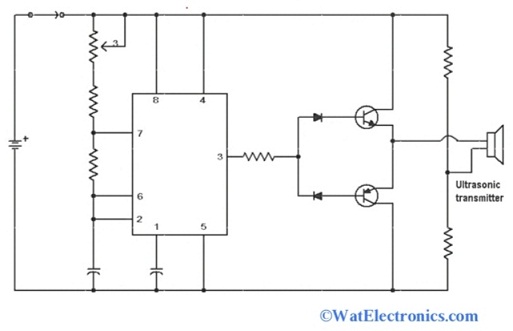
Ultrasonic Transducer Transmitter
After hitting the ultrasonic waves to the target, the ultrasonic transducer receiver receives the signals and transforms them into electrical signals. The ultrasonic transducer receiver circuit diagram is shown below.
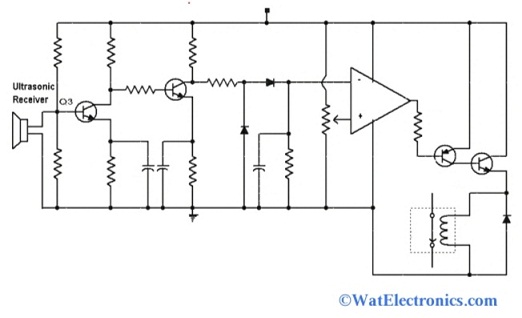
Ultrasonic Transducer Receiver
Ultrasonic Transducer Types
There are different types of transducers based on important factors such as footprint, frequency, and arrangement of a piezoelectric crystal. The following are the efficient ultrasonic transducer types given below.
Linear type: In this type of transducer, the array of a piezoelectric crystal is linear.
Phased Array: This type of transducer has a limited footprint and low frequency ranges from 2MHz-7MHz
Standard: It is also known as Normal Ultrasonic Transducer or Convex Ultrasonic Transducer. The shape of a piezoelectric crystal is curvy in this type. It is mostly preferred for in-depth test applications.
There are various types of transducers for non-destructive testing such as Delay Line Transducers, Angle Beam Transducers, Contact Transducers, Immersion Transducers, and Dual Element Transducers.
Please refer to this link to know more about Ultrasonic Sensor MCQs
Advantages & Disadvantages
The advantages of ultrasonic transducers include the following.
- They can measure any kind of material and sense any type of substance.
- They are not affected by temperature, water, dust, or any other.
- They will operate in a relevant condition under any environment.
- These are important to measure high sensing intervals.
Some of the ultrasonic transducer disadvantages are as follows,
- These are sensitive to immediate and high variations in temperature
- The change in the ability of detection is due to the unpredicted temperature conversions.
- Difficult to determine the reflections from the small targets, which are too soft and thin. However, new experiments are going on to address these problems.
Applications
The various applications of Ultrasonic Transducer include,
- Used in different fields like industrial, medical, etc.
- Ultrasonic waves are used to detect the target and measure the distance between the object and the target.
- Used to identify the location of the object and evaluate the target’s state.
- In the medical field, these transducers are used in diagnostic tests, and surgical applications like cancer treatments, internal organs testing, heart checkups, eye, and uterus checkups.
- In the industrial sector, these transducers are used to determine the distance of the specified target to prevent collisions, management of product line, liquid level controlling and monitoring, detection of wire break, detection of vehicles and people for counting, and many more.
Thus, this is all about an overview of Ultrasonic Transducer – Definition, Working Principle, Circuit Diagram, Types, Applications, Advantages, and Disadvantages. We can conclude that the ultrasonic transducer is used to determine the distance of the target by employing sound waves. To calculate the intervals, it transmits the sound wave at the desired frequency and waits for that sound wave until it receives it back. Here is a question for you, “What are the advantages and disadvantages of Ultrasonic Sensors over Ultrasonic Transducers? “