Triode for Alternating Current, or TRIAC, stands as an important semiconductor device in the realm of electronics, especially in applications where precise control over alternating current (AC) power is paramount. From dimmer switches to motor speed control systems, these devices find their place in a diverse array of applications. In This article we will look into the working principles of TRIACs, shedding light on their operational intricacies. Furthermore, we will explore the considerations and parameters crucial for selecting the right TRIAC for specific applications, ensuring optimal performance and reliability.
Understanding the Basics of TRIAC Operation:
TRIAC Symbol
The TRIAC symbol and its structure are shown below which includes three terminals like Gate and the remaining two terminals are frequently called Anode or main terminals. In the TRIAC, the gate terminal is labeled with ‘G’, and the other two anode terminals are labeled with MT1 & MT2. The Anode terminals are identical because the TRIAC component is bidirectional. The gate terminal of this device is used for controlling the device.
TRIAC Structure:
At its core, a TRIAC comprises two silicon-controlled rectifiers (SCRs) connected in inverse parallel. Each SCR is a unidirectional device, allowing current flow in one direction only. The TRIAC itself is a three-terminal device, featuring main terminals MT1 and MT2, along with a gate terminal (G).
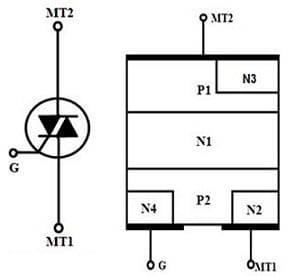
TRIAC Structure
TRIAC Working
The TRIAC triggers whenever the voltage applied at the gate terminal is higher as compared to the break-over voltage. But without making the voltage supply high, it can be triggered by providing the 35 microseconds gate pulse to turn it on. Once the applied voltage is below the break-over voltage, the gate-triggering method is used to turn it on. TRIAC operates in four different modes which are discussed below.
Whenever the MT2 terminal and Gate terminal of TRIAC is Positive to the MT1 terminal then the current will supply throughout the P1N1P2N2 path. Here, P1N1 & P2N2 are forward biased although N1P2 is reverse biased TRIAC is operated in a positively biased region. Positive gate to MT1 forward biases P2-N2 and breakdown occurs.
When the MT2 terminal is positive although the gate terminal is negative to the MT1 terminal, then current supplies throughout the P1N1P2N2 path but, the P2N3 path is forward biased & current carriers will inject into P2 on the TRIAC.
Whenever both the MT2 & gate terminals are negative concerning the MT1 terminal, then the current will supply throughout the P2N1P1N4 path. Here, two P2N1 & P1N4 junctions are forward biased although the N1P1 junction is reverse biased. So the TRIAC will be in the negatively biased region.
Whenever the MT2 terminal is negative but the gate terminal is positive to the MT1 terminal then current flows throughout P2N1P1N4. So the P2N1 & P1N4 are forward biased which results in carrier injection so turn on the device.
States of Operation:
Off State:
The TRIAC starts in the Off state, effectively acting as an open circuit with no current flowing between MT1 and MT2.
Forward Blocking State:
Upon the application of a small gate current, the TRIAC transitions into the Forward Blocking state. In this state, the device blocks current until a specific voltage threshold, known as the breakover voltage, is reached.
Conduction State:
Once the breakover voltage is surpassed, the TRIAC enters the Conduction state, becoming a low-resistance path for current flow in either direction. This state persists until the AC falls below a certain threshold.
Controlled Triggering:
To control the point at which the TRIAC enters the Conduction state within each half-cycle of the AC waveform, a controlled triggering mechanism is employed. A brief pulse of current is applied to the gate terminal at a specific point in the AC cycle, determined by electronic circuits. This controlled triggering enables precise phase control and modulation of AC power.
Bidirectional Control:
A distinctive feature of TRIACs is their bidirectional nature, allowing them to conduct current in both directions. This bidirectional control capability is fundamental to their role in managing power in both halves of the AC cycle.
Turn-off Mechanism:
The TRIAC remains in the Conduction state until the AC passing through it falls below a certain level, often at the zero-crossing point. At this juncture, the TRIAC turns off, resetting the cycle.
Switching Circuit using TRIAC
TRIAC is a three-terminal AC switch that is frequently used for AC power control like in ceiling fans speed regulators, AC bulb dimmer circuits, and many more. Here we are going to discuss a simple switching circuit using TRIAC for understanding how it practically works.
The required components to make this switching circuit using TRIAC mainly include; a TRIAC, 100 Ohms resistor, 12V bulb, and a switch. Connect the circuit as per the diagram shown below.
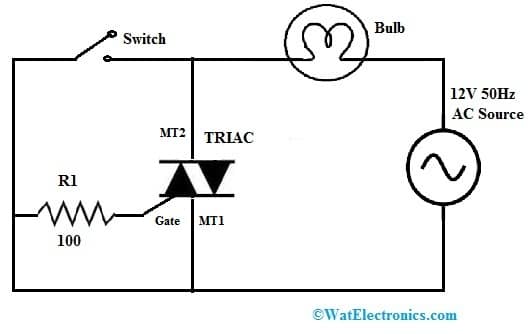
Switching Circuit Diagram with TRIAC
Working
The TRIAC in this circuit plays a key role in turning ON & OFF an AC load with a switch. After that, the 12V 50Hz mains power source is connected to a small bulb using the TRIAC. Whenever the switch within this circuit is closed the phase voltage is provided to the TRIAC’s gate pin through the R1 resistor. If the applied gate voltage is more than the threshold voltage of the gate terminal, then the current flows throughout this pin is higher than the gate threshold current.
Once the switch is pushed the gate pin of TRIAC gets the gate voltage & consequently, the TRIAC will turned ON. The load-like bulb in the circuit will glow only if the switch in the circuit is pushed. When the switch is released, then TRIAC will be in latched condition, but since the i/p voltage is AC then current flow throughout the TRIAC will go under the holding current & so the TRIAC will be turned off.
How to Choose a TRIAC:
Selecting the right TRIAC is a critical step in ensuring the efficiency and reliability of electronic applications. Various parameters must be carefully considered to match the TRIAC with the specific requirements of the application.
A. Voltage Rating (Vdrm/Vrrm):
The voltage rating of a TRIAC (Vdrm/Vrrm) is fundamental, representing the maximum voltage the device can withstand in its off-state. It is imperative to select a TRIAC with a voltage rating exceeding the maximum voltage in the application, accounting for fluctuations and transient voltage spikes.
B. Current Rating (It):
The current rating (It) is a key factor, indicating the maximum current the TRIAC can handle. Both continuous and peak current requirements should be considered. Choosing a TRIAC with a current rating meeting or exceeding the application’s demands prevents overheating and ensures reliable operation.
C. Gate Trigger Current and Voltage (Igt and Vgt):
The gate trigger current (Igt) and voltage (Vgt) are crucial for the proper triggering of the TRIAC. Ensuring compatibility with the control circuit is essential. The control circuit must provide the necessary gate trigger current and voltage for reliable switching.
D. Holding Current (Ih):
The holding current (Ih) is the minimum current required to keep the TRIAC in the conducting state after triggering. It is vital to ensure that the load current is sufficient to maintain this holding current, preventing unintentional turn-off and erratic behavior.
E. Gate Power (Pgt):
Gate power (Pgt) represents the power required to trigger the TRIAC. The control circuit should be capable of supplying this power for reliable and consistent switching. Compatibility between the control circuit and the TRIAC is essential for optimal performance.
F. Critical Rate of Rise of On-State Current (di/dt) and Off-State Voltage (dv/dt):
For applications with rapidly changing currents or voltages, the critical rates of rise of on-state current (di/dt) and off-state voltage (dv/dt) become significant. Choosing a TRIAC with appropriate di/dt and dv/dt ratings is crucial to prevent stress on the device and ensure stable operation.
G. Package Type:
These are available in various package types (TO-220, TO-218, TO-252, etc.). The choice depends on mounting and thermal requirements. Factors such as available space, heat dissipation, and ease of assembly influence the selection of the package type.
H. Temperature Ratings:
The operating temperature range of the TRIAC is critical for reliability and longevity. Selecting a TRIAC that can operate within the application’s temperature conditions is crucial. Operating outside the specified temperature range may lead to degraded performance and reduced lifespan.
I. Repetitive Peak Off-state Voltage (Vdrm) and Repetitive Peak Reverse Voltage (Vrrm):
These parameters specify the maximum voltage the TRIAC can block in the off-state, particularly essential for bidirectional applications. Both Vdrm and Vrrm should exceed the maximum voltage in the application to ensure proper blocking capability.
TRIAC VI Characteristics
The VI (Voltage-Current) characteristics of a TRIAC (Triode for Alternating Current) illustrate how the device responds to changes in voltage and current across its terminals. TRIACs operate in four quadrants, and each quadrant represents a different combination of voltage polarities and gate triggering. Understanding the characteristics in each quadrant is essential for designing and analyzing circuits involving TRIACs.
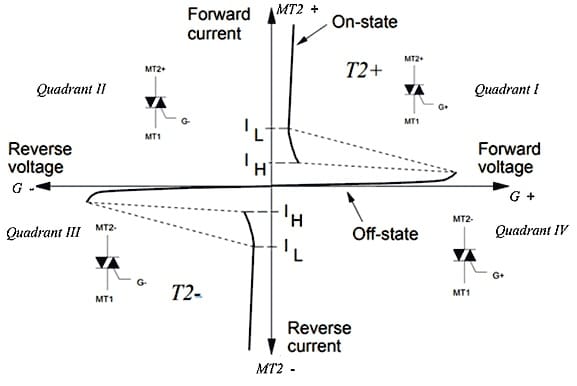
TRIAC VI Characteristics
Quadrant I (QI) – Positive Voltage, Positive Gate Triggering:
- Off State (Cut-off Region):
- In QI, the voltage between MT1 and MT2 is positive, and positive gate triggering is applied.
- The TRIAC remains in the Off state until the voltage exceeds the breakover voltage.
- The VI characteristics show a negligible current until the breakover voltage is reached.
- Forward Blocking State:
- After the breakover voltage, the TRIAC enters the Forward Blocking state.
- The VI curve shows a gradual increase in current as the voltage continues to rise, indicating the device is in the Forward Blocking state.
- Conduction State:
- When the gate is triggered positively, the TRIAC enters the Conduction state, and the current rises sharply.
- The VI curve in this region reflects the low voltage drop across the TRIAC during conduction.
- Reverse Blocking State:
- In QI, there is no reverse voltage, and the TRIAC does not exhibit reverse blocking characteristics.
Quadrant II (QII) – Negative Voltage, Positive Gate Triggering:
- Off State (Cut-off Region):
- In QII, the voltage is negative, but positive gate triggering is applied.
- The VI characteristics show negligible current until the voltage exceeds the breakover voltage.
- Forward Blocking State:
- Similar to QI, the TRIAC enters the Forward Blocking state after the breakover voltage is surpassed.
- Conduction State:
- Positive gate triggering allows the TRIAC to conduct, and the VI curve exhibits a sharp increase in current.
- Reverse Blocking State:
- There is no reverse voltage in QII, and the TRIAC does not exhibit reverse blocking characteristics.
Quadrant III (QIII) – Negative Voltage, Negative Gate Triggering:
- Off State (Cut-off Region):
- In QIII, both the voltage and gate triggering are negative.
- The VI characteristics show negligible current until the voltage exceeds the absolute value of the breakover voltage.
- Forward Blocking State:
- The TRIAC enters the Forward Blocking state once the absolute value of the breakover voltage is surpassed.
- Conduction State:
- Negative gate triggering allows the TRIAC to conduct, and the VI curve exhibits a sharp increase in current.
- Reverse Blocking State:
- There is no reverse voltage in QIII, and the TRIAC does not exhibit reverse blocking characteristics.
Quadrant IV (QIV) – Positive Voltage, Negative Gate Triggering:
- Off State (Cut-off Region):
- In QIV, the voltage is positive, but gate triggering is negative.
- The VI characteristics show negligible current until the voltage exceeds the breakover voltage.
- Forward Blocking State:
- The TRIAC enters the Forward Blocking state after the breakover voltage is surpassed.
- Conduction State:
- Negative gate triggering allows the TRIAC to conduct, and the VI curve exhibits a sharp increase in current.
- Reverse Blocking State:
- There is no reverse voltage in QIV, and the TRIAC does not exhibit reverse blocking characteristics.
A TRIAC does not have a distinct reverse blocking state. Unlike a unidirectional device such as a diode or a rectifier, which exhibits a clear reverse blocking state, a TRIAC is bidirectional and conducts in both directions once triggered.
In Quadrants I and III (positive gate triggering), the TRIAC conducts when the voltage between its main terminals (MT1 and MT2) reaches the breakover voltage. In Quadrants II and IV (negative gate triggering), the TRIAC conducts when the absolute value of the voltage exceeds the breakover voltage.
However, when the voltage across the TRIAC is reversed (opposite polarity), it does not actively block the current. Instead, it behaves as a low-resistance path in the reverse direction, allowing current to flow. This bidirectional conduction is a distinctive feature of TRIACs.
In the context of TRIAC operation, the term “absolute value of voltage” refers to the magnitude or numerical value of the voltage, irrespective of its polarity. The absolute value is always positive. This concept is important when considering negative gate triggering in Quadrants II and IV.
When using negative gate triggering in a TRIAC, the device conducts when the absolute value of the voltage across its main terminals (MT1 and MT2) exceeds the breakover voltage. In other words, whether the voltage is negative or positive, the TRIAC conducts if the magnitude of the voltage exceeds the specified threshold.
For example, if the breakover voltage of a TRIAC is 20 volts, negative gate triggering would cause the TRIAC to conduct when the voltage (in either direction) exceeds 20 volts in magnitude. So, a -30V or +30V voltage would trigger the TRIAC to conduct because the absolute value of both is 30 volts, surpassing the 20-volt breakover threshold.
This bidirectional triggering characteristic is essential for the versatile control of alternating current (AC) in both halves of the AC cycle, making TRIACs suitable for applications such as dimmer switches, motor control, and other power control systems.
Understanding the VI characteristics in each quadrant is crucial for designing and implementing TRIAC-based circuits. These characteristics guide engineers in selecting appropriate triggering methods and optimizing performance based on the specific requirements of the application, whether it involves motor control, lighting systems, or power regulation.
Advantages & Disadvantages
The advantages of TRIAC are discussed below.
- These can be turned ON with positive polarity or negative polarity of gate signals.
- A single component is used mainly for complete switching.
- It can switch both AC waveform halves.
- It needs a single heat sink only.
- It needs a fuse for protection.
- A secure breakdown in any direction is achievable.
- Once the voltage supply is decreased to zero then TRIAC will turn OFF.
The TRIAC disadvantages include the following.
- These are not reliable as compared to silicon-controlled rectifiers.
- Its (dv/dt) rating is lower.
- It doesn’t fire on both sides of the waveform symmetrically.
- Switching provides an increase to the maximum range of harmonics because of nonsymmetrical switching.
- Lower ratings are available as compared to SCR.
- We have to be cautious regarding the triggering circuit because it can be activated in any direction.
- These are less sensitive within the third quadrant operation, which leads to problems by reliable triggering.
- It is not appropriate for DC applications.
Applications/Uses:
Understanding the theoretical aspects of TRIAC operation and selection is crucial, but practical insights into real-world applications enhance comprehension. Here, we explore a few common applications of TRIACs and how their unique characteristics contribute to the functionality of these systems.
A. Dimmer Switches:
It plays a pivotal role in dimmer switches, allowing users to control the brightness of lighting systems. The controlled triggering mechanism of TRIACs enables precise adjustment of the phase angle, regulating the amount of power delivered to the light source.
B. Motor Speed Control:
In motor speed control applications, TRIACs facilitate the management of AC power to adjust the speed of motors. The bidirectional control capability allows for smooth modulation of power, influencing the rotational speed of the motor.
C. Heating Control Systems:
Heating control systems, such as those in ovens or electric stoves, leverage TRIACs for precise control over the amount of power delivered to the heating element. The ability to modulate power in both directions contributes to maintaining a stable and controlled temperature.
D. Power Supplies:
TRIACs find applications in power supplies where controlled AC power is required. By adjusting the triggering angle, TRIACs enable the regulation of output voltage, contributing to the stability of the power supply.
Advanced Considerations and Emerging Trends:
As technology advances, so does the landscape of semiconductor devices. In the realm of TRIACs, advancements continue to enhance performance and open doors to new possibilities. Exploring these advancements provides a glimpse into the future of TRIAC technology.
A. Smart and IoT Integration:
The integration of TRIACs with smart and Internet of Things (IoT) technologies is on the rise. Smart home systems, for instance, can benefit from the precise control offered by TRIACs, allowing users to remotely adjust lighting and other AC-powered devices.
B. Enhanced Efficiency and Miniaturization:
Advancements in semiconductor manufacturing contribute to the development of more efficient and compact TRIACs. These developments lead to devices with improved heat dissipation, reduced power losses, and increased reliability, making them suitable for a broader range of applications.
C. Application-Specific Designs:
Manufacturers are increasingly offering application-specific TRIACs designed to meet the unique requirements of specific industries or applications. These specialized devices may feature optimized characteristics, such as higher voltage ratings or faster switching speeds, catering to the evolving needs of diverse sectors.
D. Environmental Considerations:
As sustainability becomes a focal point in engineering and technology, TRIAC manufacturers are exploring ways to reduce the environmental impact of their devices. This includes the development of TRIACs with enhanced energy efficiency and eco-friendly manufacturing processes.
The TRIAC stands as an indispensable component in electronics, enabling precise control over AC power in many applications. Understanding the operational principles of TRIACs, coupled with a meticulous consideration of parameters during the selection process, ensures optimal performance and reliability.
From the fundamental states of operation to the intricate details of voltage and current ratings, each aspect contributes to the effectiveness of TRIACs in diverse applications. Real-world examples showcase the practical implications of TRIACs in dimmer switches, motor speed control, heating systems, and power supplies.
Check your understanding by answering few of our questions in TRIAC MCQs.
Looking ahead, the integration of TRIACs with smart technologies, ongoing advancements in efficiency and miniaturization, and the development of application-specific designs signal a promising future for these semiconductor devices.