Proximity sensor comprises all sensors that execute non-contact detection as compared to limit switches that notice objects through contacting physically them. These types of sensors change the data into an electrical signal on the movement or occurrence of a target. These sensors are used in mobile phones. Once the target is in a small range, then the lock screen of the mobile user interface will come into view which is called sleep mode. These sensors can be utilized to identify air gestures through the collection of proximity sensing elements.
The main purpose of this sensor is to notice the object without any physical contact with it. The utmost distance detected by this sensor is called a normal range. This kind of sensor produces an electromagnetic field otherwise utilizes IR radiation to generate a light beam. This article discusses an overview of proximity sensors and their working.
What is a Proximity Sensor?
A non-contact sensor that is used to detect the presence of a target or object is called a proximity sensor. This sensor is capable of detecting close-by objects through electromagnetic radiation beams or electromagnetic fields without any physical contact. The detection of the target can be done based on the kind of proximity sensor by using light, sound, electromagnetic fields, IR, etc.
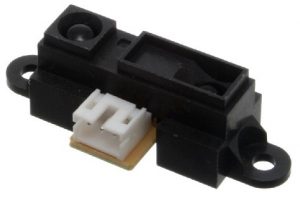
Proximity Sensor
This sensor is most frequently used in mobile phones, so the role of the proximity sensor in mobile is to detect a nearby person. For instance, an IR proximity sensor is used in mobile phones to detect a human ear when the operator places the phone on the ear, then the mobile display will be turned off automatically, so power consumption can be reduced.
Working Principle
A non-contact sensor like a proximity sensor detects the existence of a target once it enters the field of the sensor. The detection of a target can be done based on the kind of sensor by using light, sound, IR otherwise electromagnetic fields.
These kinds of sensors are utilized in recycling plants, phones, anti-aircraft systems, assembly lines & self-driving cars. There are different kinds of proximity sensors available where each sensor detects targets in dissimilar methods.
Proximity Sensor Types
There are different kinds of proximity sensors used in different applications but each type of sensor detects an object in a different way they are inductive proximity, capacitive proximity, ultrasonic proximity, and optical proximity. But the most frequently used proximity sensors are inductive proximity & capacitive proximity.
Inductive Proximity Sensor
These are contactless sensors used for detecting metal objects. This kind of sensor mainly depends on the induction law. Once a metallic object approaches it, then it drives an oscillator through a coil. This sensor includes two versions & includes four essential components which are discussed below.
The versions of inductive proximity sensors are unshielded and shielded
Shielded Version
In the shielded version, the generated electromagnetic field is concentrated in the face, where the sensor coil sides are covered up
Unshielded Version
In the unshielded version, the generated electromagnetic field through the sensor coil is clear, so it allows for wider & greater detecting distances. Inductive proximity sensor includes four major components like an oscillator, coil, Schmitt trigger, & output switching circuit.
When an AC is provided to the sensor coil, an electromagnetic detection field can be generated. Once a metal object is placed near the magnetic field, then eddy currents can be formed & result in coil inductance alters. Once coil inductance alters, then the circuit will change the output switch of the sensor which is monitoring continuously.
Here whenever a target is not there, these sensors oscillate continuously and when an object is there then only the switch will trigger. The inductive proximity sensor is mainly used for industrial and security purposes like metal object detection, land mines, automation machine production, etc.
Capacitive Proximity Sensor
These types of sensors are also contactless, used to notice both the objects like metallic & non-metallic that includes powders, liquid, granular, etc. This sensor works by noticing a change within capacitance.
Likewise to inductive type, it includes an oscillator, switching circuit for output & Schmitt trigger.
The main difference is it includes two charging plates like one internal & one external for capacitance. The connection of these two plates can be done like this; the internal plate is connected to the oscillator whereas the external plate is used as the detecting surface.
This kind of proximity sensor generates an electrostatic field. Once an object reaches the detecting region, then both plate’s capacitance also increases those results in amplitude gain of an oscillator. This gain activates the output switch of the sensor. These sensors oscillate only once the target is present.
The applications of capacitive proximity sensors include Industrial processes, controlling moisture, touch applications, etc
Ultrasonic Proximity Sensor
These sensors are one kind of proximity sensor that is utilized in several applications of automation as well as manufacturing. The main purpose of this sensor is to detect objects and measurement of distance. These sensors are used in processing beverages, food & several packaging applications.
The frequency range of these sensors is higher than the audible sound of humans approximately 20 kHz. The basic principle of this sensor is to transmit an ultrasonic signal & gets a signal back. By using the time disparity among these signals, the distance toward the target can be decided.
An ordinary design for both the transmitter & the receiver within the similar physical housing, even though they can also be placed in separate units such as certain photoelectric sensors through separate detectors & emitters. Arranging the transmitter & receiver within the same unit can reduce the cabling and installation.
These sensors use sound instead of light, so they can be utilized wherever these sensors have complexity like detecting plain plastic labels and objects, surfaces with extremely reflective that discard optical sensors. These are also resistant to general contaminants like moisture, ambient light & dust.
Optical Proximity Sensor
Generally, these sensors are cost-effective as compared to inductive & capacitive types. These are applicable in automated systems as they can arrange into small locations. These sensors are also called light beam sensors.
An optical proximity sensor contains a sensor and a light source. A sensor is used to detect the light whereas a light source produces light. The light sensor in this sensor is normally a semiconductor device like a photodiode that produces less light once light energy strikes it.
There are different types of proximity sensors available like through-beam, retro-reflective & diffuser. The applications of optical proximity sensors mainly include computer alarm systems, copy machines, light fixtures, etc.
Magnetic Proximity Sensor
The magnetic proximity sensor simply detects the magnetic field based on mechanical principles. They detect the presence of a magnetic target which is characterized through its magnetic field. Once it enters the range of the sensor detection, then it activates the switching procedure.
These sensors are mainly used for detecting non-contact locations away from the typical ranges of inductive sensors. The operating principles used by this sensor are GMR inductive, reed switches, magnetoresistive, variable reluctance otherwise Hall Effect sensors.
Features
The features of the proximity sensor include the following.
- Contactless sensing allows this sensor to detect without touching the object, ensuring the object waits well-conditioned
- These sensors are almost unaffected through outside colors of targets because it detects simply physical changes
- These kinds of sensors are applicable for broad temperature range usage & damp conditions different from your usual optical detection.
- These sensors are used in android and IOS based mobiles. It includes simple infrared technology that activates and deactivates the display based on your usage. For instance, it deactivates your mobile display once a phone call is continuing such that you wouldn’t start something accidentally while placing it close to your ears
- Longer service life as compared to other sensors
- Response rate speed is high
How to Check Proximity Sensor?
On every phone, the proximity sensor is the main feature but sometimes its role cannot be understated in our devices. This sensor mainly assists gestures & notices our facial features on phones. Some of the most frequently reported sensor problems to include the following that may occur because of Software otherwise Hardware issues.
- The mobile screen will go dark while speaking on phone.
- After the call ends, the screen of the mobile remains dark.
- Sometimes, face unlock doesn’t work properly
Verify whether your mobile goes into sleep mode while making calls, the sensor will be immobilized and enters into sleep mode. So in this condition, push the power switch to activate the mobile screen back on. If the error happens in other situations, determine the position of the sensor. This will be changed through the mobile model.
To fix the above issues, here are some solutions.
- Need to check for dirt otherwise a fracture on the sensor’s screen.
- Take away screen guard & check
- Need to restart your mobile
- Need to update your mobile
- Reset mobile
- And finally, visit a mobile service center
Proximity Sensor Circuit
An infrared proximity sensor is one kind of electronic device used to notice the existence of a target once it comes to a fixed range from this sensor throughout reflected IR rays. Here this circuit is built with a normal operational amplifier like LM358.
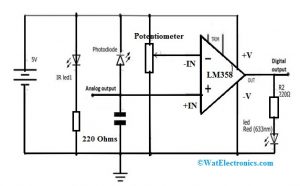
Proximity Sensor Circuit Diagram
The essential components used to build this circuit are
- IR led
- Power supply ranges from 5 v – 6v.
- IR Photodiode
- Resistors 220 ohms -2 & 10k ohm-1
- IC LM358 Op-amp
- Red led
- Preset
The working principle of this circuit is quite easy. A typical idea includes two LEDs that are parallel to each other to the target like a photodiode & IR emitting led. Both these act like a pair of transmitter-receiver. Once an obstruction approaches before emitter waves, they are reproduced back & interrupted through the receiver.
According to the photodiode propertied, the interrupted IR waves will reduce the resistance of the photodiode and the resultant electric signal is generated. This signal in practice is the voltage across the 10k resistor which is directly fed to the non-inverting end of the op-amp.
The operational amplifier’s main function is to evaluate the two inputs specified to it. The photodiode signal can be given to pin 3 (non-inverting) & the potentiometer’s threshold voltage can be given to pin 2 (inverting pin). If the voltage is higher at the non-inverting pin as compared to the inverting pin voltage then the output of an op-amp output is high or low.
Here in this circuit, the operational amplifier changes the signal from analog form to digital. The output of the sensor can be used in two forms like analog & digital. Analog output values range continuously from zero to finite value. This signal directly cannot be given to the motor drivers as well as other switching devices.
Primarily, they have to be processed through the microcontrollers & changed into digital form using analog to digital converter. This form of output needs an extra microcontroller however removes the use of an operational amplifier.
The form of digital output is available either low or high. The proximity sensor’s digital output signal is mainly useful to prevent the motion of the robot which is used for avoiding obstacles. Once an obstacle comes near to the robot, then the signal can be directly given to the motor driver‘s input pins to prevent the motors.
Applications
The proximity sensor uses/proximity sensor applications are listed below.
- The proximity sensor is mainly used to notice the existence of any target without touching.
- It detects as well as calculates any changes within the nearby location.
- These are utilized in mobile phones
- This kind of sensor is mainly used within the automation system of the home to switch on the light automatically once any person there within the room.
- These are used in machine tools, rolling mills & automation systems.
- This sensor is used to count the objects which are moving in the conveyor belt.
- This sensor is used for measurement of speed, direction rotation measurement of electrical motors & distance measurement of vehicles.
- The photoelectric proximity sensor is mainly used for plastic object detection.
- Inductive proximity type is used to detect metal objects
- The ultrasonic proximity sensor is used for the measurement of the distance from the target
- IR proximity type is used to count different applications.
- Capacitive proximity type is used for the non-ferrous objects detection, little weighted objects as they provide more accuracy as compared to others.
- Proximity sensors like inductive and photoelectric are mainly used for detecting position.
Please refer to this link to know more about Hall Effect MCQs & Ultrasonic Sensor MCQs.
Please refer to this link to know more about Color Sensor & Gyroscope Sensor.
Thus, this is all about an overview of proximity sensors and their working with applications. The advantages of proximity sensor are; it doesn’t include mechanical parts, so the lifespan of this sensor is high, reliability is high; the working principle is simple circuits are simple and low-cost devices. The applications of this sensor mainly include position, detection, automated machine counting, inspection, consumer products, and robotics. Here is a question for you, what are the disadvantages of proximity sensors?