In fluid power circuits, pressure is an essential factor. A pressure transducer is used to change the pressure of a fluid into an electrical signal to check & control the pressure within electronic control systems. Once these transducers are connected to a suitable electrical source then it will generate an electrical output signal like current frequency or voltage which is proportional to the force.
There are different kinds of transducers are available which are used to generate linear output through the pressure applied as well as other system variables. Most of the outputs are V, mV, mA. This article discusses an overview of a pressure transducer and its working.
What is a Pressure Transducer?
A pressure transducer is also known as a pressure transmitter. The main function of this transducer is to change the pressure or force into an analog electrical signal. Even though these are classified into different types but the most frequently used transducer is a strain gauge.
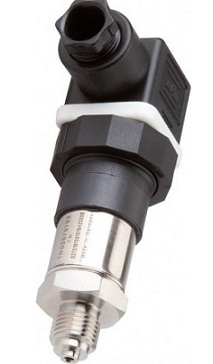
Pressure Transducers
Here strain gauges’ physical deformation plays a major role in converting the pressure into electrical signal because these are connected to the transducer’s diaphragm as well as connected in the configuration of a Wheatstone bridge. The force applied to this transducer generates the diaphragm deflection that launches strain to the gages. The strain gauge will generate an electrical resistance that is proportional to the force.
Pressure Transducer Working Principle
The structure of the pressure transducer includes a force collector namely an elastic diaphragm as well as a transduction component that uses an inductive, dependent resistive, capacitive technique to generate an electrical signal.
Pressure transducers use strain gauges to compute the pressure that operates on them. The strain gauges resist deformation to generate a difference within voltage. Here, the measurement of pressure mainly depends on the amount of difference detected within the voltage.
There are excellent pressure transducers also available that use piezoelectric or capacitance sensors instead of strain gauges. These are mainly preferred depending on the work environment, range & estimated accuracy from the transducer.
Types of Pressure Transducer
There are different types of pressure transducers based on their measurement like the following.
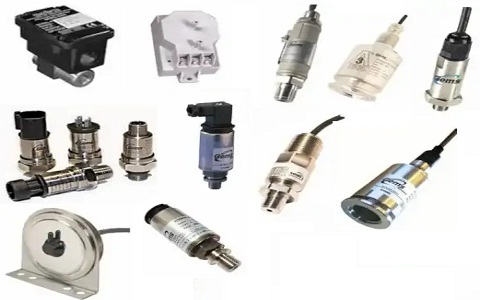
Types of Pressure Transducer
Strain Gauge
Strain gauge pressure transducer is mainly used to gauge very low, high & differential pressures. Here, differential pressure is nothing but the variation within pressure among any two specified points. This kind of transducer includes an element for detecting namely a diaphragm. Any diaphragm deformation will cause the resistance change for the strain gauges.
Usually, in a Wheatstone bridge, there are four gauges are used to enhance the transducer’s sensitivity. So, this resistance change is changed into the utilizable output signal.
Capacitance
This kind of pressure transducer is used to measure the pressure through sensing the changes within electrical capacitance because of the diaphragm movement. This capacitance transducer includes a diaphragm, two capacitor plates & an electrode that is connected to an unpressurized face.
The arrangement of these two plates can be done at a fixed distance with each other, & the modification within pressure will extend the space in between these two plates. The capacitance change can be converted into a utilizable signal. So based on the application, the pressure transducer can calculate either gauge, absolute otherwise differential force.
Potentiometric
A potentiometric pressure transducer includes an exact potentiometer that includes a wiper and is connected to a diaphragm element. The deflection on the diaphragm will change the wiper position. The value of resistance will be changed among the wiper as well as one finish of the potentiometer. The resistance value is the measure of the applied pressure.
Resonant Wire
This type of transducer includes a vibrating wire that is positioned within a diaphragm. The oscillator maintains the wire vibrating. When the pressure is modified within the diaphragm, then it will affect the pressure of the wire as well as alters the resonant frequency. This resonant frequency can be detected through digital counter circuits for changing into an electrical signal.
Inductive
An inductive pressure transducer works on the electromagnetic induction principle. This type of transducer includes a diaphragm that is connected to a ferromagnetic core. The minor diaphragm deflection can cause the linear movement within the ferromagnetic core to induce a current. The core movement can change the induced current because of the pressure change. So the change within current can be converted into a utilizable signal.
Piezoelectric
This transducer uses a ceramic material or quartz crystal to produce an electric charge once the pressure is applied. This charge can be measured like a voltage and this voltage is proportional toward the change within the pressure. This kind of transducer is extremely responsive and sensitive.
How to Select a Pressure Transducer?
There are different types of pressure transducers available that are used for different applications. Each type of transducer includes different features that will affect its performance. When selecting a pressure transducer, the following criteria need to consider.
- Media Type
- Seal Material & Housing
- Temperature Range
- Pressure
- Transducer Type
- Hysteresis
- Repeatability
- Approvals
- Type of Measurement
- Application Type
- Range of Pressure
- Process Media
- Installation Environment
- Accuracy
- Output
Pressure Transducers Electrical Output
Generally, the electrical outputs of pressure transducers are three types like mV (millivolt), amplified voltage & 4 to 20mA. After that, it is required to change an electric o/p into an engineering unit like bars or PSI.
Millivolt Output
These are the most economical pressure transducers because they generate a millivolt output of around 30mV. The actual output is directly proportional to the pressure transducer input power or excitation. If the excitation is changed, the output will be changed because it depends on the level of excitation.
So regulated power supplies (RPSs) are recommended to utilize with mV transducers. When the o/p signal is very low, then this transducer should not be situated in an electrically loud atmosphere. The distance between the readout instrument & the transducer must be kept fairly short.
Voltage Output
Voltage output transducer comprises essential signal conditioning to provide high output as compared to mV transducer. So normally the output ranges from 0 to 5Vdc otherwise 0 to10Vdc. Even though, the transducer output is not usually a straight excitation function that means UPSs (unregulated power supplies) are frequently adequate if they fall in a particular power range.
Because they include a higher range output & these are not responsive to electrical noise like millivolt pressure transducers. So, they can be used in industrial surroundings through a comparatively high range of noise.
4-20 mA Output
These transducers are called pressure transmitters. As a 4 to 20mA signal is less affected through electrical noise as well as resistance within the signal wire. These kinds of transducers are applicable once the signal transmits to long distances. It is not rare to utilize these types of transducers within applications wherever the lead wire should be 1000 feet or above
Pressure Transducer Calibration
The calibration is a procedure once the output signal of the transducer is evaluated to the measured value using a precise device, so the relationship between these two can be determined. Pressure transducers are mainly used across different applications to offer precise, real-time information on how a system is functioning.
Calibration is significant to maintain the accuracy of a pressure transducer & it is not a single procedure. So, when these transducers are used in significant applications then we must calibrate regularly to keep high performance. If this transducer drifts out of its particular force range, then it can guide to fake pressure readings so equipment performance can be decreased. Calibration permits the consumer to be confident that their transducers are properly performing & measuring the required range of pressure precisely.
Based on the type of industry, calibration regulations may rule the calibration frequency. Highly regulated industries like food and pharmaceuticals must keep a high level of accuracy to make sure everything is working correctly & to reduce any security risks.
To confirm appropriate readings in different industrial applications where precision is significant, it is best to calibrate the pressure transducer a minimum of two times a year. For instance, the industry like FDA includes some guidelines which are scheduled in affixed intervals depending on the kind of aseptic production region.
In the gas & oil industries, calibration is a major concern. Because of its unstable nature, calibration standards should be extremely changed through the management to ensure secure opportunities at all stages of distribution & production of the product. These calibration guidelines will decrease the risk of dangerous conditions like oil spills, explosions, etc.
Stability of Pressure Transducer
The stability of a transducer has a vast impact on how frequently the transducer must be calibrated.
Stability is normally mentioned on a datasheet of the transducer, sensors that are found to be extremely constant do not require to be recalibrated as often as sensors that tend to drift out of the specified range.
Users can determine the stability of a transducer by achieving a trend analysis of calibration history. Depending on these results, the interval of calibration can be expanded or reduced depending on the precision requirements of the application.
Advantages
The advantages of pressure transducer include the following.
- Economical
- Quick Response
- Robust
- Good Accuracy
- High Stability
- Regulated Output
- Suitable Linearity
- Highly Sensitive
- These are Small Size Measurement Instruments
Disadvantages
The disadvantages of pressure transducer include the following.
- These are fairly responsive to environmental conditions.
- They have modest accuracy is subject to drift or instability
- They give a late response in shock & vibration conditions
- These transducers function at a slight temperature with sluggish response & moderate accuracy.
Applications
The applications of a pressure transducer include the following.
- Pressure transducers are used in liquid power applications, which require precise &high-resolution power.
- These are applicable where measurement of force is required through a fixed digital display.
- These are applicable in closed-loop pumps for testing the operation of the pump.
- These are used as an electronically changeable pressure switch.
- Used to check the levels of gas and liquid on a variety of medical devices.
- These transducers are used to check the liquid levels within the HVAC system
- Altitude sensing for satellites & aircraft
- Fuel pressure as well brake can be monitored within vehicles with the help of brake pressure transducers.
- Water pressure transducers are used to detect the liquid range for pump stations & well
- These types of transducers are suitable in closed-loop applications
Please refer to this link to know more about Capacitive Transducer & Solar Pump.
Thus, this is all about an overview of a Pressure Transducer, its working, advantages, and its applications. The price of pressure transducer may vary through several factors The main differentiator is whether you can utilize a typical, off-the-shelf, or custom type. If the transducer is more accurate, the price will be high. Here are a few questions for you, what are the different types of transducers available in the market? What is an Inductive Transducer?