The various electrical machines and panels are fixed onboard to sail the ship from one place to another place very efficiently and safely. To avoid the breakdown during sailing, these machines require regular maintenance. That means, measuring electrical quantities like resistance, voltage, and current will help to analyze the proper condition of the electrical machine. For this measurement, different instruments are used like a PMMC instrument.
PMMC instruments are one of the simple and widely used onboard instruments, which can assist the electrical equipment with regular maintenance and measure the required quantities of the circuit. It is also known as Galvanometer or D’Alvanometer. This article is all about PMMC instrument construction, working, advantages, and disadvantages.
What is PMMC Instrument?
The PMMC instrument stands for Permanent Magnet Moving Coil. When the coil placed in the stationary magnetic field produced by the permanent magnet moves and exerts a mechanical torque on the moving coil, then it is called a Permanent magnet moving coil. The instrument that measures the current flowing in the coil from the pointer deflection is known as the PMMC instrument. It is also known as the D’Arsonval instrument or Galvanometer.
These instruments are used in place of voltmeter and ammeters. These are more accurate and reliable but work only for measuring DC quantities. By placing the current-carrying coil in the strong magnetic field produced by a permanent magnet, the mechanical torque acts on the coil and moves. According to the coil movement, the pointer of the instrument starts deflecting over the scale, which indicates the value of the electrical quantities that are to be measured. The pointer deflection is directly proportional to the current in the moving coil.
The basic PMMC instrument diagram is shown below. A rectangular coil of thin wire with some turns is wound on an aluminum frame, which has an iron core inside. It is placed between the U-shaped permanent magnet poles, which are made up of Alnico (magnetic alloy). The coil pivoted on the jewel bearings helps in the free rotation of the coil. To concentrate the magnetic field, two soft-iron pole pieces are attached to the poles of the magnet.
The current to be measured is fed through two control springs, one is on top and the other is below the coil. These control springs produce the control torque. The induced damping current due to the eddy current moves the coil from one position to another. The coil that carries a current placed in a strong magnetic field experiences a torque and starts moving. The value of the current being measured is indicated by the pointer attached to the spindle.
PMMC Instrument Construction
The components used in the PMMC construction are, moving coil, magnet system, control spring system, damping, pointer, and scale.
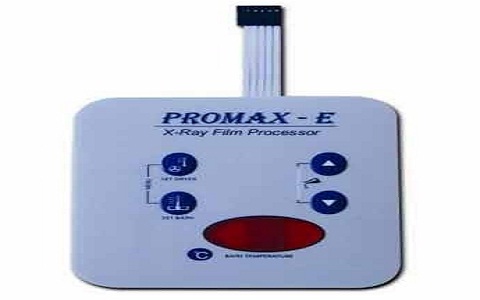
PMMC Device
Moving Coil
It is made up of copper wire with some turns and wound on an aluminium former. As the aluminium former is pivoted on the jewel bearings, the coil can move in the stationary magnetic field produced by the permanent magnet very freely. The current flowing through the coil deflects the pointer attached to it and the value of the current is measured. The radial distance and the uniform magnetic field between the poles are increased by the aluminium former.
Magnet System
It consists of permanent magnets, which produce strong stationary magnetic fields. These permanent magnets are U-shaped and made up of Alnico and Alcomax. Therefore, they can withstand high external magnetic fields and don’t lose their magnetism. The flux density and magnetic field intensity are high due to their small size.
Control Spring System
It consists of springs made up of phosphorus bronze and it is placed between the two jewel bearings. The control action of the springs produces controlling torque. They are used to allow current to flow through the coil and out of the coil. The controlling torque is opposite to the pointer deflection and equal to the magnitude of the current. The suspension of ribbon and gravity control are also the reasons to produce controlling torque.
Damping
In a PMMC instrument, the damping torque is produced due to the aluminium former movement in the magnetic field produced by the permanent magnets. The eddy current develops in the coil due to the aluminium former moment and it is opposite to the moving coil. This deflects the point to reach a steady-state position. The eddy current and the friction of the bearings are also responsible for producing damping torque.
Pointer and Scale
The moving coil in the magnetic field deflects the pointer and its deflection is directly proportional to the current flowing through the coil. The pointer is attached to the spindle and the deflection is over the gradual scale. It is made up of aluminium and is thin and lightweight. The one end of the pointer is flattened to look like a fine blade. The mirror and proper alignment of the pointer blade reduce the parallax error. The scale indicates the reading of the measured current value.
Working Principle
The PMMC instrument working principle is based on the principle of the motor. When the current-carrying coil is positioned in the magnetic field produced by a permanent magnet, then a force is experienced by the coil and moves. This is called the D’Arsonval principle. Hence the force acting on the coil due to the magnetic field is directly proportional to the current passing through the conductor/coil. The PMMC instruments are more reliable and accurate, which are used for only DC measurements.
Force on the coil is F = BIL
Where B = magnetic flux density in Wb/m2
I = current in the coil in Amps
L = length of the coil in meters
PMMC Instrument Working
The PMMC instrument working is similar to the motor working. The current through the coil when the instrument is connected to the circuit. When the current-carrying coil is placed in the magnetic field produced by a permanent magnet, then a mechanical torque acts on the coil and starts moving.
Therefore the pointer of the instrument attached to the moving coil moves gradually in a clockwise direction, which indicates the measured value of current in the circuit. The deflecting torque due to the mechanical torque is proportional to the magnetic flux density and length of the moving coil. The pointer deflection is directly proportional to the current flowing through the moving coil.
The action of the spring produces the controlling torque, which opposes the deflecting torque, and the pointer of the instrument starts deflecting in an anticlockwise direction as the current in the coil is reduced. At steady-state conditions of the PMMC instrument, the controlling torque and the deflecting torque are equal. The angle of deflection is directly proportional to the controlling torque.
At the steady-state position of the pointer, the damping torque is produced due to the eddy current. The eddy current setup on the aluminium former opposes the movement of the coil, which deflects the pointer and comes to rest position. The pointer of the instrument indicates the magnitude of the measured current. The scale is linear and uniform. This instrument is used for accurate DC measurements.
Equation Involved
When the current flows through the coil, the force acting on both sides of the coil produces the deflecting torque. Hence, the coil’s movement induces the deflecting torque. The equation involved in this instrument is the deflecting torque equation, which is determined as given below.
Consider B is the flux density in Wb/m2
‘L’ is the vertical length of the coil
‘I’ is the current flowing through the coil
‘N’ is the no. of turns of the coil
As per Fleming’s Left-hand rule, The direction of current flow and the magnetic field is perpendicular to the force F.
The formula for force F acting on the coil due to the current flow is given as,
F = NBIL
Hence, The deflecting torque Td is given as,
Td = Force x perpendicular distance
Td = NBIL x d
Td = NBILd Newtons…. Eq 1
Let the area of the coil is A= L x d
Then eq1 becomes,
Td = NBIA…. Eq 2
Mathematically, the deflecting torque equation is written as,
Td = GI … . . Eq 3
Where G = Galvanometer constant = NBA
The controlling torque Tc of the coil produced due to the spring is given as,
Tc = Kθ. …. Eq 4
Where ‘θ’ is the angle of pointer deflection
‘K’ is the spring constant.
At the steady-state condition of the instrument, the deflecting torque is equal to the controlling torque.
Form eq 3 and eq 4 we get,
Td = Tc
GI = Kθ
Therefore, θ = GI / K
From the above equation, we can conclude that the deflection of the pointer in the PMMC instrument is directly proportional to the current flowing through the coil. The scale is uniform for linear current/voltage measurements in DC circuits.
What are the Different Reasons that Cause an Error in PMMC?
3 different reasons cause an error in PMMC Instrument.
Error due to Temperature
As the temperature changes, the resistance of the moving coil changes, which causes an error in the output reading of the PMMC instrument. The temperature coefficient of the copper wire in the moving coil is 0.04°C rise in temperature. The rate of temperature rises very fastly due to the lower temperature coefficient of the moving coil. Hence the resistance increases and causes an error.
Error due to Spring
An error in the output reading of the PMMC depends on the contortion (twisting or bending) and quality of the spring. The pointer of the PMMC instrument doesn’t show the accurate reading due to the ageing of spring and hence causes an error. The error caused by the permanent magnets and the errors caused by the ageing of spring are opposite to each other and they can be compensated.
Error Due to Ageing of Permanent Magnets
The ageing of permanent magnets is due to the loss of their magnetism with time. And also the effect of heat and vibration reduces the magnetic strength and coil deflection results in an error in the PMMC reading.
To overcome these errors, the swamping resistance is connected to the moving coil in series. Where the swamping resistance is the resistor that has a low-temperature coefficient. This swamping resistance reduces the effect of temperature on the coil.
Please refer to this link to know more about PMMC Instrument MCQs
Advantages
The advantages of PMMC Instrument are as follows,
- It is more accurate and consumes low power.
- The torque to weight ratio is high
- No occurrence of hysteresis losses
- The linear scale of the instrument is divided uniformly, which measures the quantities very easily and accurately. Since the current is directly proportional to the pointer deflection.
- Eddy current damping is very efficient and effective
- The effect of external stray fields on the instrument reading is very little.
- It is used to measure several quantities with different shunts and multipliers.
- Reduced bearing friction due to controlled deflecting torque.
Disadvantages
Some of the disadvantages of the PMMC instrument are listed below,
- It is used to measure only DC but not AC
- Fragile construction
- Its cost is high when compared to moving iron instruments
- Errors occur in the reading due to the ageing of permanent magnets and control spring, due to the temperature changes, and due to friction.
Please refer to this link to know more about Measurement & Instrument MCQs
Applications
The few applications of PMMC Instrument are given below,
- It is used in the measurement of direct voltages and currents
- Used to detect small currents in DC galvanometers.
- It is used to measure the change in magnetic flux linkage in Ballistic galvanometers
- It is used as an Ammeter
- It is used as a Voltmeter
- It is used as an Ohm meter
- It is used as a Galvanometer.
- At low frequencies, the PMMC instrument along with the rectifier is used to measure AC by converting into DC (<1mA)
Thus this is all about an overview of a PMMC instrument – definition, diagram, construction, working principle, working, advantages, disadvantages, and applications. Here is a question for you, “What are the differences between PMMC instruments and Moving Iron type Instruments? “