Ultrasonic sensors are one of the fascinating technologies that rely on sound waves. These sensors emit high-frequency ultrasonic pulses (beyond the range of human hearing) and measure the time it takes for these pulses to bounce back after hitting an object. By knowing the speed of sound in the medium (usually air) and the time taken for the sound waves to return, the sensor can accurately calculate the distance to the object. Ultrasonic sensors have gained widespread popularity in various applications due to their ability to accurately measure distances using sound waves. In this article, we will delve into the factors that need to be considered to choose an ultrasonic sensor comparing them to other types of sensors and explaining why they are a preferred choice in many scenarios.
Factors to be Considered while Selecting an Ultrasonic Sensor
To choose an ultrasonic sensor, there are many factors that need to be considered which are discussed below.
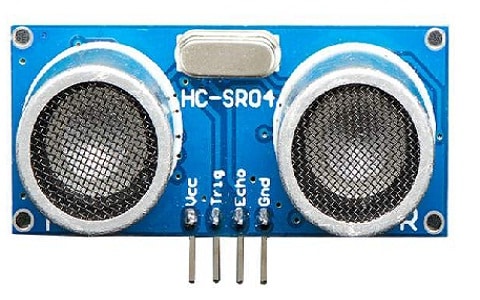
How to Choose an Ultrasonic Sensor
1. Precision Distance Measurement
Ultrasonic sensors excel at providing precise distance measurements. This precision can be crucial in various applications, such as robotics, industrial automation, and autonomous vehicles. Unlike some other sensors that might have limitations in accuracy, ultrasonic sensors offer consistent and reliable distance data.
2. Range
One of the defining characteristics of ultrasonic sensors is their range. These sensors are available in a wide range of models, each with a specific maximum range. For instance, the MB1240 might have a range from 20cm to 765cm. This flexibility in range allows you to choose a sensor that suits your particular application, whether you need to measure short distances or scan larger areas.
3. Resolution
Resolution refers to the smallest increment of distance that a sensor can detect. Ultrasonic sensors are known for their high resolution, meaning they can provide precise measurements even for objects that are very close together. This feature can be particularly advantageous in applications where distinguishing between nearby objects is essential.
4. Interface Options
Ultrasonic sensors typically offer various interface options, including analog, digital, and serial communication. This versatility allows for easy integration with microcontrollers and other devices. Depending on your project’s requirements, you can select a sensor with the interface that best suits your needs.
5. Size and Form Factor
The physical size and form factor of a sensor can be critical in many applications, especially those with limited space. Ultrasonic sensors are generally compact and come in various shapes and sizes to accommodate different installation requirements. This makes them highly adaptable to a wide range of scenarios.
6. Accuracy and Precision
While accuracy and precision are related, they are not the same. Accuracy refers to how closely a sensor’s measurements align with the true value, while precision relates to the consistency and repeatability of measurements. Ultrasonic sensors often offer high accuracy and precision, making them suitable for demanding applications where reliable data is essential.
7. Operating Environment
Ultrasonic sensors can be designed for specific operating environments. Some models are optimized for indoor use, while others are built to withstand outdoor conditions. Features like weatherproofing and rugged construction can extend the sensor’s lifespan and ensure reliable performance in harsh conditions.
8. Output Options
Beyond distance measurement, some ultrasonic sensors can provide additional information, such as temperature or humidity data. These additional outputs can be valuable in applications that require environmental monitoring alongside distance measurement.
9. Customizable Parameters
Many ultrasonic sensors allow users to adjust various parameters to optimize their performance for specific applications. These parameters can include beam width, sampling rate, and filtering options. Customizability enhances the sensor’s versatility and adaptability to different use cases.
10. Ease of Integration
The ease with which a sensor can be integrated into a project is a crucial factor for engineers and developers. Ultrasonic sensors are well-supported by various development platforms and libraries, simplifying the integration process. This support, combined with their flexible interface options, makes them a preferred choice for many applications.
Comparison with Other Sensors
To appreciate the unique features of ultrasonic sensors like the MB1240, it’s essential to compare them with other types of sensors commonly used for distance measurement and object detection. Here, we’ll briefly discuss some of the key differences and considerations when choosing between ultrasonic sensors and alternatives:
Ultrasonic Sensors vs. Infrared (IR) Sensors:
Infrared sensors, such as IR distance sensors and LiDAR (Light Detection and Ranging) sensors, also measure distances. However, they use infrared light instead of sound waves. Ultrasonic sensors have an advantage in terms of range and are less affected by lighting conditions. IR sensors can be more suitable for indoor applications where reflective surfaces are common.
Ultrasonic Sensors vs. Laser Distance Sensors:
Laser distance sensors, often referred to as laser rangefinders, offer high precision and accuracy. They are commonly used in applications requiring extremely precise measurements, such as surveying and construction. However, they can be expensive and may not be as suitable for applications with limited budgets or where precision is not a top priority.
Ultrasonic Sensors vs. Capacitive Sensors:
Capacitive sensors measure changes in capacitance to detect the presence or absence of an object. While they excel at proximity sensing and can detect non-metallic objects, they may not provide accurate distance measurements as consistently as ultrasonic sensors, especially over longer distances.
Ultrasonic Sensors vs. Time-of-Flight (ToF) Sensors:
ToF sensors, often found in smartphones for gesture recognition and depth sensing, rely on measuring the time it takes for light or laser pulses to travel to an object and back. While ToF sensors offer fast and accurate distance measurements, they are typically limited in range compared to ultrasonic sensors.