A Control system is a method of connecting devices so that we can manage, direct and control the behavior of other devices using control loops. Apparently, it is a system that controls other systems. Control systems are classified as Linear control systems and Non- Linear control systems, Analog or continuous systems, Digital or Discrete systems, single input single output systems, Multiple inputs multiple-output systems, etc.. . The control system that follows the principle of homogeneity and additivity is known as Linear control system. Hence, the systems that do not follow the homogeneity principle are known as Non-linear Control systems. One of the classifications of the control system is the Closed-loop control system.
What is a Closed-Loop Control System?
Closed- Loop control systems are also known as Feedback Controllers. Here, the operation of the controller is monitored and controlled using a feedback loop. The aim is to maintain the value of the process variable the same as that of the setpoint value.
Any error in the value is detected and the value is sent through a feedback loop to the controller. Now the operation of the controller is either increased or decreased accordingly. Due to the use of this feedback loop, which is called a control loop, closed-loop controllers are known as Feedback controllers. For a linear feedback system, the control loop consists of sensors, a control algorithm, and actuators.
Block Diagram of Closed-Loop Control System
The below figure shows the block diagram of a closed-loop control system.
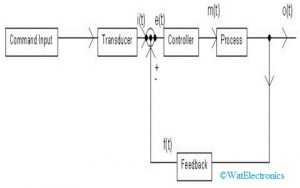
Block Diagram
In a closed-loop control system, the output of the system controls the input of the system to obtain the desired functionality from the system. This increases the accuracy of the system. Closed-loop systems are fully automatic systems.
A closed-loop control system consists of command input, Transducer, controller, process, feedback element. The command input is given to the transducer. To change the input form according to the nature of the controller, the command input is given to the transducer. The signal from the transducer is applied to the controller. Depending on the applied input signal, the controller generates a control signal. According to the generated signal required action takes place in the system and specific output is produced.
To check whether the generated output is the same as desired output, a part of the signal is given back to the input. This is the feedback signal. When this feedback signal is compared with the reference input signal an error signal is generated. This error signal is applied to the controller. The controller then produces a manipulated control signal that guides the process in eliminating the error present in its output. Hence, the desired output is obtained at the end of the process.
This cycle repeats itself and continuously monitors the process output so that the desired output level is maintained. Hence,closed-loop control systems are considered fully automated systems.
Characteristics Equation
The below figure is used to derive the characteristics equation of the closed-loop control system.
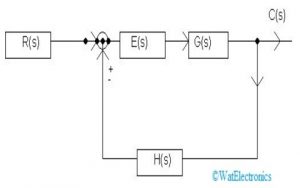
Characteristics Equation
The characteristics function of a system gives the mathematical relation between input and output of the system. The behavior of a system can be understood by its characteristics equation.
The gain of the system is given as the ratio of its output to the input. Thus, from the above figure,
C(s) = E(s)*G(s) ——-Eqi 1
But we know the input signal to the controller is the difference between the applied input signal and the feedback signal. Whereas feedback signal is the fraction of output signal. Hence, the Eqi 1 can be written as
E(s) = R(s) – H(s).C(S)
From Eqi 1
C(S) = [R(S) – H(S)C(S)]*G(S)
C(S) = R(S)G(S) – H(S)C(S)G(S)
R(S)G(S) = C(S) + H(S)C(S)G(S)
R(S)G(S) = C(S)[1+H(S)G(S)]
C(S)/R(S) = G(S)/[1+G(S)H(S)], this is for the Characteristics function of a closed-loop control system with negative feedback
Characteristics equation of a closed-loop control system with positive feedback is given as:
C(S)/R(S) = G(S)/[1-G(S)H(S)]
Different Types
Based on the feedback loop of the closed-loop control system, they are classified into two types. They are a Closed-Loop control system with Negative feedback and a Closed-Loop control system with Positive Feedback.
Positive Feedback System
In this type of control system, the feedback signal is in in-phase with the input signal. Here, the reference signal is added to the feedback signal. This increases the overall gain of the control system.
Negative Feedback System
In this type of control system, the feedback signal is out of phase with the input signal. Here the reference signal is subtracted from the feedback signal to get the error signal. This reduces the gain of the overall system.
Examples of Closed-Loop Control System
Some of the basic examples of this control system are Automatic Iron System, Temperature control system, etc…
The main aim of the system is to maintain the constant temperature of the water. In this system water is provided with a constant flow to the system, the internal valve is used to generate steam that is mixed with water to maintain the desired temperature of the water. A pressure thermometer is used as feedback for this system.
When a reference input is provided, the valve generates a control signal that indicates the system to generate the required amount of steam. This steam is mixed with the water and the water is moved towards the outlet. The pressure thermometer measures the temperature of the water at the outlet and compares it with the reference input value.
If no difference is found between the two temperatures a control signal is generated to stop the flow of steam. If variations are found between two temperature values, the controller generates a control signal to increase or decrease the stream levels to remove the error. This process is repeated continuously and the constant temperature values are maintained.
Advantages
Some of the advantages of a closed-loop control system over an open-loop control system are as follows:
- It reduces error in the output by automatically adjusting the system’s input.
- This system improves the stability of a system.
- It controls the sensitivity of the system to external factors.
- This control system enhances the robustness of the system.
- It produces reliable and repeatable performance.
- This system also reduces the disturbance compared to the open-loop control system.
- Improved reference tracking
Disadvantages
The disadvantages of a closed-loop control system over an open-loop control system.
- This system many times requires a complex design with more than one feedback path to get the desired outputs.
- The controller becomes unstable and starts to oscillate when the gain of the controller is too sensitive to the changes in its input signal.
- This system is very expensive.
Applications
Some of the applications of the closed-loop control system are as follows:
- Automatic toaster.
- Automatic washing machine
- Air conditioner
- Automatic water level controller in water tanks
- DC Motor speed controller.
- Home heating
- Missile launching system.
- Boiler control
- Car’s cruise control
Know more about Distributed Control System.
Control theory was in place even before world war 2. Wright brothers used the concept of dynamic control to control their flight. The theory of discontinuous control systems was discovered and applied in the areas of fire control systems, guidance systems, electronics, etc. Today’s control system has found its way into the field of AI. It is being used in the development of chatbots. voice-support helplines, etc. To overcome the limitations of the open-loop control system, the closed-loop control system was introduced. What is the transfer function of a closed-loop control system with positive feedback?