In automobiles, engine knocking is a sound or detonation or engine ping that occurred due to high-frequency vibrations caused by poor quality fuel, wrong spark plug, irregular ignition /explosion occurring in the cylinder, and deposits on the cylinder wall. These engine knocks can cause power wastage of the engine and destroy the engine. These days, modern vehicles are equipped with various sensors to monitor their functioning like measuring the air, temperature, etc. In addition to these, the knock sensors are also installed to track and maintain the vibration and sound levels of the vehicle’s engine. This article gives a brief description of the knock sensor located in the vehicle engine.
Knock Sensor Definition
An electronic control system of the engine Or listening device on the engine that detects the vibrations and sounds coming from the engine block or due to the engine knocking and converts into electrical signals and sends them to the Engine Control Module (ECM) is called the knock sensor. It is also known as a piezoelectric sensor Or vibration sensor.
The system in the automobile evaluates the data in the ECM and determines whether the ignition timing should be adjusted or not. To prevent the damage, it can illuminate the CEL (check engine light) and turn OFF the component in the engine.
When an electrical signal is received by the ECM, it retards the ignition or ignition timing and stops the knocking in the engine. The voltage of the electrical signal generated by this sensor depends on the knocking intensity. So this sensor safeguards the engine by transmitting a knock signal to the ECM.
This is because the detonation time harms the engine, and the high temperatures and vibrations that occur during the explosion might damage the engine parts. The knock sensor is bolted to the cylinder block (engine block) or cylinder head.
Knock Sensor Working Principle
The knock sensor works on the principle of the piezoelectric effect by using piezoelectric elements or piezoelectric ceramics. The piezoelectric elements can generate voltage when vibration or pressure is applied to them. Piezoelectric ceramics are materials (quartz, gallium phosphate, tourmaline) that can convert mechanical effects like pressure, vibration, or movement into an electrical signal and vice versa.
Due to the electro-mechanical effect of the piezoelectric ceramics, these are widely used in watches, ultrasonic power transducers, motion sensors, ultrasonic cleaning, lithotripters, ultrasonic welding, loudspeakers with high-frequency, active vibration dampeners, actuators in atomic force microscopes and many more. The knock sensor circuit diagram is shown in the figure below.
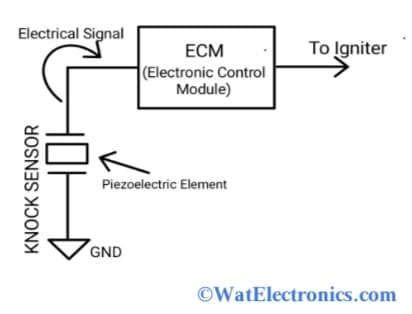
Knock Sensor Circuit Diagram
A piezoelectric element can detect the vibrations caused by engine knock and send an electrical signal to the ECM. The ECM retards the ignition timing when it receives a certain voltage signal from the engine. As a result, ignition starts closer to TDC (Top Dead Centre) than before, which reduces the internal engine’s tendency to knock. The knock sensor stops knocking by reducing the pressure and maximum temperature inside the engine by decreasing the ignition timing.
The piezoelectric element of the knock sensor is tuned to detect the knock frequency of the engine. The knock sensor generally consists of a piezoelectric crystal (piezoelectric element), a shunt resistor, and a screw/thread on one end of the knock sensor that allows the device to be screwed into the block close to the piston. The basic structure of the knock sensor is shown in the figure below.
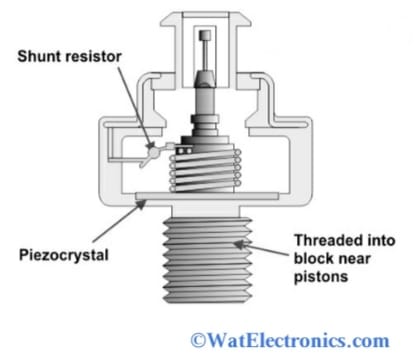
Structure of Knock Sensor
How to Test a Knock Sensor with a Multimeter?
If a knock sensor fails, then it usually causes one or more severe symptoms. There are several ways to check if the sensor is working properly. Here are some methods you should follow before vehicle driving. Otherwise, if the sensor is damaged, the results will be even worse and the engine may fail in working.
The testing process of this sensor is categorized into 2 methods. In the first method, the knock sensor is checked by visual inspection of parts, checking cable assembly for any damage, and some precautions are to be taken. And the second method is testing with a multimeter as shown below.
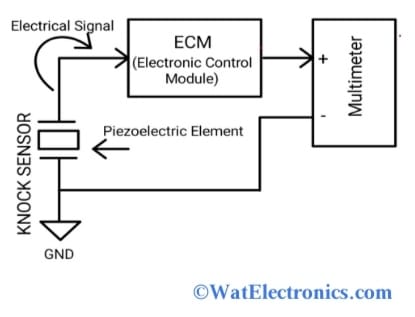
Testing with Multimeter
Now let’s know how to test a knock sensor with a multimeter. The components required are; Multimeter, ECU, and a Knock sensor.
- First, apply the handbrake and stop the engine. If the engine is very hot, wait until it cools down.
- Now open the hood and when it opens, start the engine. This is a precaution to avoid opening the hood while the engine is running.
- After starting the engine, locate the vehicle’s knock sensor on the engine manifold. It is usually installed towards the center of the engine under the intake manifold.
- Bring the manual of the vehicle (car), which explains all the precautions to take when looking for the knock sensor to avoid damage.
- Locate the cable assembly with the knock sensor.
- Pull the wire harness from the base to the knock sensor to disconnect it from the knock sensor.
- Take a multimeter and connect the wires (leads) to the knock sensor. Connect the multimeter’s negative terminal to the ground and positive terminal to the signal wire (positive) of the knock sensor. If the knock sensor is not faulty and working properly, the multimeter will show resistance. The multimeter should show a resistance value in the range of 93 to 110K Ohms.
- Regular inspection of vehicles is necessary. To avoid unpredictable vehicle damages during long travel, the knock sensor and some critical components must be inspected.
Please refer to this link to know more about interfacing a knock sensor to a microcontroller.
Types of Knock Sensor
Knock sensors detect irregular engine vibration due to uneven combustion. Two methods are commonly used to detect engine knocking. They are vibration measurement & measurement of pressure. Most of these sensors work according to the 1st method. Vibration detection sensors are available in three types according to the detection mechanism. They are; Inductive resonant sensors, Piezoelectric resonant sensors, and piezoelectric non-resonant sensors.
Inductive and Piezoelectric Resonant Sensor :
It consists of a vibration plate with the same resonant frequency as the shock/vibration of the knock. If the knocking occurs, then the plate reaches its maximum vibration amplitude and is converted into an electrical signal due to the effect of electromagnetic induction or the piezoelectric effect. Due to the narrow band response, the resonant sensor can only detect certain engine knock frequencies.
Piezoelectric Non-resonant Sensor
This type uses a spring method to measure vibration directly, so the frequency band (typically 5 kHz to 15 kHz) is wider. Knock frequency can vary slightly with engine speed, so non-resonant sensors generally perform better than resonant sensors. Vibration-based knock sensors are usually mounted on the cylinder block or cylinder head.
Pressure Sensor
This is another sensor to detect knocking in an engine to directly measure the pressure in the cylinder. The pressure sensor is usually built into the spark plug by attaching a ring-shaped piezoelectric element to a washer. Engine knocking generates noise with high frequency, that is superimposed on the normal combustion pressure waveform. Knock detection is done by filtering these signals.
Knock Sensor Failure Causes
The following are the causes for knock sensor failure.
- The knock sensor might fail due to the sensing wire damage.
- When it is not installed correctly.
- Gets damages due to the drop.
- Due to hammering while loosening.
- Due to a lack of engine power.
- When an audible knocking sound is produced continuously, it might get damaged.
- It’s a sign of damage when the warning light of the engine glows.
- Less acceleration and more combustion of fuel is another cause of knock sensor damage.
Knock Sensor Solved Problems
A faulty knock sensor usually causes one or more visible symptoms and should be solved using some techniques suggested by an automobile engineer. The most common knock sensor problems are,
Illuminated check engine light: This is the most common sign of a knock sensor problem. When the PCM detects a problem with the knock sensor or its circuitry, the module illuminates the check engine light and stores the appropriate Diagnostic Trouble Code (DTC) in memory.
Pinging noise from the engine: If the engine knock sensor is faulty, the PCM will not be able to detect or correct ignition/spark knock. As a result, you may hear metallic sounds coming from the engine. The noise is often most noticeable when the engine is overloaded.
Poor engine performance: A faulty knock sensor can also cause the ECM to misfire, resulting in poor engine performance.
How to solve knocking problems in the engine using a Knock sensor?
The main problem that can be solved by using the knock sensor is the reliable detection of knocking for more torque and less combustion. “Knock” occurs when the fuel-air mixture reignites. Prolonged knocking mainly damages the cylinder head gasket and cylinder head.
This sensor detects the high-frequency vibration characteristics of the knock engine and sends a signal to the control unit. The goal is to achieve maximum power output by starting the ignition as quickly as possible. Engines with these sensors reduce fuel consumption and increase torque.
This sensor detects vibrations caused by knocking or misfiring and sends a signal to the engine control computer to adjust the time and clear the knock.
When the engine block or engine knocking is intimated by this sensor, then it must be prevented by lowering the compression ratio, higher octane fuel, and changing the driving habits of mechatronics.
This sensor generates an AC signal that is sent to the engine computer, often referred to as the ECM. When the ECM detects a spark knock, the module retards the ignition timing until the knock disappears.
Advantages
The knock sensor advantages are,
- It can stop the knocks and kicking tendency in the engines
- Reduces power wastages.
- Improves the economy of fuel.
- Increases the torque output.
- Senses the vibration in the engine.
- Enhances the horsepower.
- Can secure the components of the engine from being damaged due to knocking.
- Unburnt gas emissions can be reduced.
- Enhances the performance of the engine.
Disadvantages
A few knock sensor disadvantages are given below.
- The noise generated during the knocking can reduce the accuracy.
- Time-to-Time maintenance is necessary.
- Expensive.
- Complexity is high.
- Replacement is required when it fails from time to time, which is very expensive.
Applications
A few knock sensor applications are listed below.
- Used in automotive industries.
- Controls the knocks in internal combustion engines.
- Used in the protection of machine tools.
- Used in cavitation detection.
- Used to monitor pivot bearings.
- Used in anti-theft systems.
- Used in the construction of machinery engines.
- Used in security applications like door knocking systems.
- Used to control the internal ignition of vehicles, especially in cars.
Thus, this is all about an overview of the knock sensor working and its types. It is usually screwed into the engine block or manifold. However, the exact location depends on the vehicle. You should refer to the repair database or repair manual to determine the exact location of the knock sensor for your application.