Electrostatic Discharge (ESD) poses a significant threat to electronic devices and integrated circuits. ESD events can generate high voltages and currents, potentially causing irreparable damage to sensitive components. Implementing robust ESD protection is crucial in ensuring the reliability and longevity of electronic systems. One key component in ESD protection circuits is the diode. This article we will look into the essential factors to consider before diode selection for ESD protection, providing a comprehensive guide for engineers and designers.
Understanding Diode Selection for ESD Protection and Its Implications
Before diving into diode selection, it’s crucial to understand the nature of ESD and its potential consequences. ESD occurs when two objects with different electrical potentials come into contact and then separate, creating a static charge imbalance. When this charge is discharged, it can result in a high-voltage spike that poses a severe threat to electronic components.
The effects of ESD can range from immediate failure to latent damage, impacting the long-term reliability of electronic devices. To mitigate these risks, ESD protection components, such as diodes, are incorporated into electronic circuits to divert and absorb the energy generated during an ESD event.
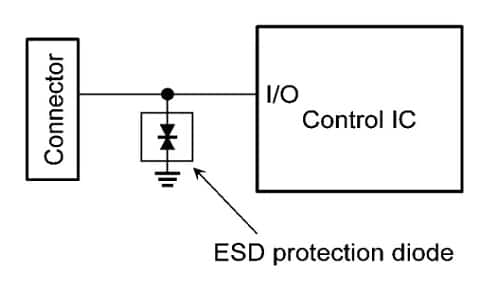
Diode Selection for ESD Protection
Key Parameters for Diode Selection for ESD Protection
1. Fast Response Time
Fast response time is a critical characteristic of diodes used in ESD protection. ESD events happen in microseconds, and a slow-reacting diode might not be able to clamp the voltage quickly enough to prevent damage. Look for diodes with low capacitance and low reverse recovery time, ensuring a rapid response to transient events.
2. Low Clamping Voltage
The clamping voltage is the voltage drop across the diode during an ESD event. A lower clamping voltage is desirable, as it limits the voltage that reaches the protected circuitry. When selecting a diode, consider its Vc (clamping voltage) specifications, and choose a diode that can effectively limit the potential across the protected components.
3. Low Leakage Current
A low reverse leakage current is crucial to avoid additional power consumption during normal operation. A diode with low leakage current helps maintain the integrity of the protected circuit by not introducing unnecessary current flow. This parameter is particularly important for battery-powered devices and other low-power applications.
4. Breakdown Voltage (V_BR)
The breakdown voltage of the diode should be well above the maximum expected operating voltage of the protected circuit. This ensures that the diode remains in its non-conducting state during normal operation but activates promptly during an ESD event, diverting excess energy away from sensitive components.
5. Temperature Stability
The diode should exhibit stable performance across the expected temperature range of the application. Temperature stability is crucial for reliable and consistent protection, especially in environments with varying temperatures. Ensure that the diode’s characteristics are well-maintained over the entire temperature range of your application.
6. Physical Size and Package
Consider the physical size and package of the diode, ensuring it is suitable for the application. Surface-mount diodes are often preferred for compact and modern electronics, while through-hole packages might be used in certain situations. The choice of package can impact the ease of integration into the overall circuit design.
7. Bi-Directional or Uni-Directional Protection
Depending on the application, you might need a unidirectional diode (protects against ESD from one direction) or a bidirectional diode (protects against ESD from both directions). Ensure the diode’s polarity matches your protection requirements to effectively safeguard the components from potential damage.
8. Compliance with Standards
Check if the diode complies with relevant ESD protection standards, such as IEC 61000-4-2. Compliance with industry-recognized criteria ensures that the diode meets the requirements for effective ESD protection. It provides confidence in the diode’s ability to safeguard electronic components against ESD events.
9. Integration with Other Protection Components
Consider how the diode will integrate with other protection components in your system. Resistors and capacitors may be added to form a complete ESD protection network. Understanding how these components work together is crucial for designing a robust and comprehensive ESD protection strategy.
Types of Diodes for ESD Protection
Several types of diodes are commonly used for ESD protection, each with its specific characteristics. Understanding the distinctions between these diodes can aid in selecting the most suitable option for a given application.
1. Schottky Diodes
Schottky diodes are known for their fast switching speed and low forward voltage drop. These characteristics make them suitable for ESD protection applications where a rapid response is essential. However, Schottky diodes may have higher leakage currents compared to other types, so careful consideration is needed in low-power applications.
2. Zener Diodes
Zener diodes operate in the reverse breakdown region, maintaining a relatively constant voltage across their terminals. They can be employed for ESD protection by clamping the voltage at a specific level. Zener diodes are bidirectional and can be suitable for applications where consistent clamping voltage is critical.
3. Transient Voltage Suppressor (TVS) Diodes
TVS diodes are specifically designed for transient voltage suppression and are commonly used for ESD protection. They have a low breakdown voltage, providing an efficient clamping mechanism during transient events. TVS diodes can handle multiple ESD events without degradation, making them a reliable choice for ESD protection circuits.
Application Considerations:
1. Specific Industry Requirements
Different industries may have specific requirements for ESD protection. For example, the automotive industry often has stringent ESD standards to ensure the reliable operation of electronic components in vehicles. Understanding these industry-specific requirements is essential when selecting diodes for ESD protection.
2. Customized ESD Protection Circuits
In some cases, a generic ESD protection diode may not be sufficient, and a customized ESD protection circuit may be necessary. This could involve combining multiple diodes, resistors, and capacitors to create a tailored solution that meets the specific needs of the application.
3. Testing and Validation
Before finalizing the selection of a diode for ESD protection, it is advisable to conduct thorough testing and validation. Real-world testing under simulated ESD conditions can help ensure that the chosen diode effectively protects the circuit against potential damage. Testing should consider factors such as multiple ESD events and different environmental conditions.
4. Cost Considerations
While ensuring effective ESD protection is crucial, cost considerations are also important. Balancing the performance of the diode with the overall cost of the electronic system is essential for achieving an optimal solution. It’s important to weigh the benefits of enhanced protection against the budget constraints of the project.
Case Studies and Practical Examples
To illustrate the principles discussed above, let’s explore a couple of case studies where diodes were selected for ESD protection in specific applications.
Case Study 1: Consumer Electronics
In the design of consumer electronics, where compact size and low power consumption are critical, Schottky diodes with fast switching characteristics and low forward voltage drop may be preferred. The choice of a unidirectional or bidirectional diode depends on the nature of potential ESD events in the application. Surface-mount packages are often chosen for their space-saving benefits.
Case Study 2: Automotive Electronics
Automotive electronics require robust ESD protection due to the challenging environment and stringent industry standards. TVS diodes with low breakdown voltage and high surge current capability may be selected for their ability to handle multiple ESD events and transient conditions. Additionally, bidirectional protection might be necessary to safeguard against potential ESD events from different directions.
Thus, diode selection for ESD Protection is a critical aspect of designing reliable electronic systems. Engineers and designers must carefully consider factors such as response time, clamping voltage, leakage current, breakdown voltage, temperature stability, and compliance with standards. Additionally, understanding the specific requirements of the industry and application, along with the integration of other protection components, contributes to the overall effectiveness of the ESD protection strategy.
As technology continues to advance, the demand for more robust ESD protection solutions will persist. Diode manufacturers continue to innovate, providing engineers with a diverse range of options to meet the unique challenges posed by ESD. By staying informed about the latest developments in diode technology and adhering to best practices in ESD protection design, engineers can ensure the reliability and longevity of electronic devices in an increasingly interconnected and electronic world.